Dies are specialized machine tools used in the automotive industry to press sheets of metal into shapes (e.g. car doors). Die spotting is a process for refining these tools during development – so named because of a blue paste that colours the metal and forms spots of lesser blue colour to show where the tool must be optimized. Die spotting is currently performed manually, therefore highly inefficient and human error prone. This technology is a software to digitize the die spotting process.
START:IP
Technologie Kurzbeschreibung (nur Englisch)
Software for Automotive Die Spotting
Software for Automotive Machinery Tool (Die) Spotting
Bookmark4
Die tools are intended for mass manufacturing of car parts, and therefore the development process is incredibly important to ensure an optimized tool that will produce high quality parts time and time again. The trial and error process for optimizing dies is a huge source of both time delay and costs, especially because the die spotting is performed manually by a spotting expert. The role of this expert is to examine the blue colouring by eye and then identify parts of the tool that must be adjusted (polished or ground) accordingly. It is an iterative process, with the goal of achieving homogeneous blue colouring on the pressed metal form. An image of this die spotting with homogeneous colour is an industry requirement for the tool to be permitted for use.
This technology takes advantage of 3D scanning technology, already in place in most die manufacturers, to generate a point cloud image of the blue-stained formed sheet metal. It can then analyse the blue colour – indicating where it is homogeneous and where it is not with a greater precision than the human eye. Using such technology could reduce the number of iterations required to optimize the die, and therefore the time and costs for die development.
This technology takes advantage of 3D scanning technology, already in place in most die manufacturers, to generate a point cloud image of the blue-stained formed sheet metal. It can then analyse the blue colour – indicating where it is homogeneous and where it is not with a greater precision than the human eye. Using such technology could reduce the number of iterations required to optimize the die, and therefore the time and costs for die development.
If you click the button and fill out the form to be „matched“ with a technology, we will introduce you to the scientist / transfer manager of the respective research institution. In this way, you immediately have the chance to receive more detailed information and to start discussions about a possible joint project.
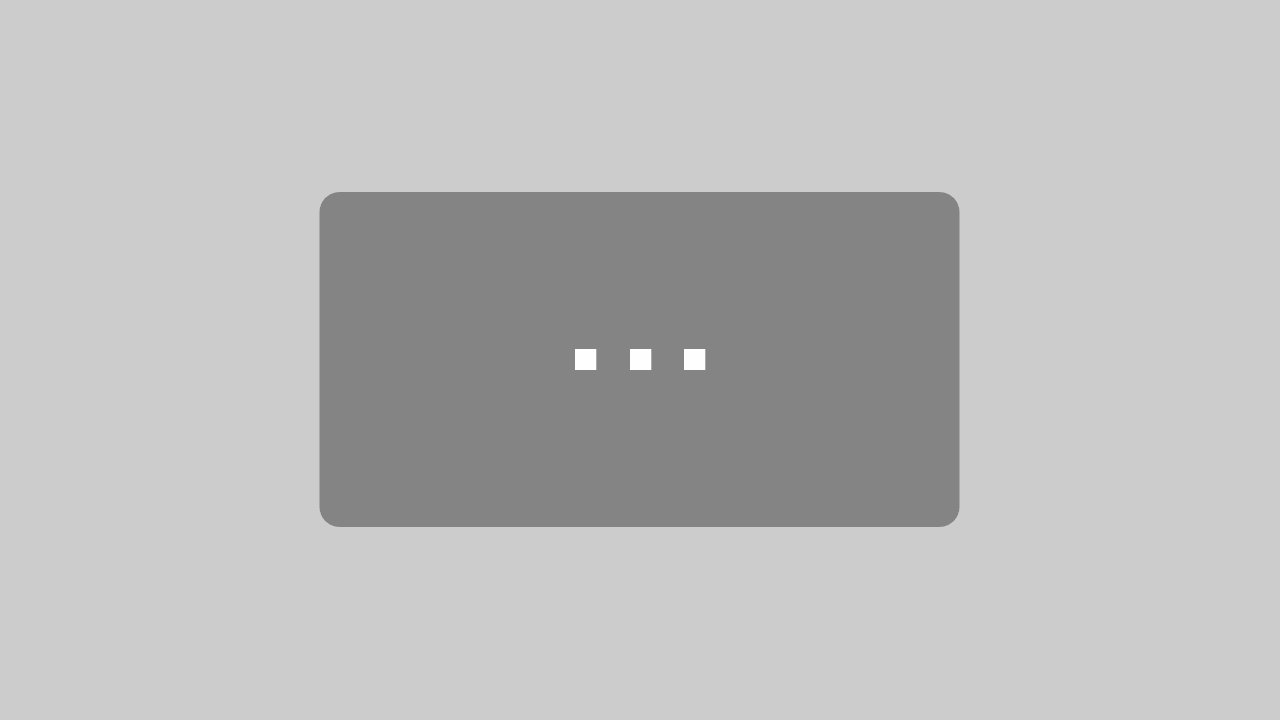
Mit dem Laden des Videos akzeptieren Sie die Datenschutzerklärung von YouTube.
Mehr erfahren